Who Should Be the Control Account Manager (CAM) for Direct Material?
When Earned Value is applied to Government sponsored programs via the EIA-748 guidelines, all program resources must be accounted for in the EV data elements. These include direct labor, materials and subcontracts as well as applicable indirect costs.
Important to this discussion, EV considers material to be just another resource of the program and as such, there are a few basic assumptions underlying the treatment of that material.
First, it’s assumed that the company has a purchasing/procurement capability consistent with good business system practices (and Federal requirements). EV also assumes that an adequate inventory control capability exists that properly assigns/tracks materials to a program, whether it be from a program specific inventory account, or a “common” account that serves as the source for multiple programs.
Finally, EV assumes that materials are costed appropriately to a program and that any instances of “borrow/payback” do not inappropriately benefit one program at the expense of another.
Given these assumptions, this series of articles focuses on the direct material element and some of the key considerations, including:
- Who should be the Control Account Manager (CAM) for direct material for a program?
- What’s the most appropriate method to earned value for material?
- When should we use earned value for it?
- When are the actual costs for the material assigned to the program Control Account (CA)'s?
The topic in this first article addresses the first question: Who should be the CAM for direct material for a program?
To answer this question, we must review the major questions a CAM seeks to resolve:
- Who should define/finalize and own the scope of work for the Control Account (CA)?
- Who should define the resources and the sequence/timing required to execute that scope?
- Who is best suited to exert control over the resources performing the work?
- Who should have the information necessary to status progress of the work and forecast its completion?
- If cost and/or schedule performance deviates from the plan, who should know and why?
- Who is best able to define future requirements for resources, i.e., estimate-to-complete forecasting?
These represent the principal responsibilities of a CAM, and in a typical contractor organization, the answer to these questions more often than not points us at two potential organizations: Engineering or Procurement/Supply Chain Management.
In a design/development program, it is typically the Engineering organization who is key to these CAM functions. They are the ones who have identified the need for a material item and know when it is needed in the context of the overall CA effort. Engineering relies on the Supply Chain organization to provide the preliminary cost estimates and then to exercise the procurement process, but it's Engineering that has identified the material needed and knows when it is needed to support CA scope.
Thus, the responsible engineering discipline lead, i.e., structural, mechanical, electrical, etc. is the logical CAM for the work, both labor and the associated material, on a specific lowest level WBS element. In order for this to work effectively requires timely communications between the Engineering CAM and Supply Chain counterparts regarding final prices, delivery dates, etc. so that the CAM has all of the information necessary to effectively support management.
Some contractors, however, decide that the Supply Chain organization, due to control and work authorization considerations, is the most appropriate owner of the material required to support the Engineering CA. This can also work well so long as the CAM and the Engineering discipline lead act as a coordinated team regarding all aspects of planning, progress updating and forecasting regarding the material items.
In a production environment, it is likely a different outcome when we look at CAM responsibilities. It’s neither the Engineering nor Supply Chain organizations who accomplish the requisite planning and control functions for program materials. Rather, the Production Control organization and the material requirements planning (MRP) systems drive material needs and ordering dates; production plans; progress updates and analysis; and forecasting of future material resource necessary to support efficient line flow. Thus, the most likely location of the CAM is in a Production Control organization.
There may be legitimate exceptions to my approach to identifying the CAM for material in your organization, but if you focus on the traditional duties of a CAM it should steer you in the right direction. In summary, the CAM for program direct material should be the individual who has responsibility for planning and controlling the material resource being applied to a lowest level WBS element.
What do you think? Do you agree or disagree? Let us know in the comments below.
Not sure what this means for your organization? to discuss.
Topics: Aerospace & Defense, Energy, Utilities, Oil & Gas, Earned Value Management (EVM), Integrated Program Management (IPM), Technology, Deltek PPM, Government & Public Sector, Microsoft EPM, forProject Technology
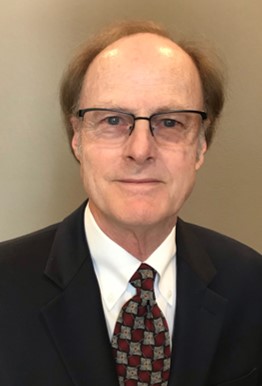
By Jim Wrisley
Jim is a Senior Associate at Pinnacle. He has over 45 years of experience in the field of program/project management, with special emphasis in Earned Value Management Systems (EVMS). Jim has managed many EVMS design, implementation, and training engagements for clients performing on major aerospace, defense, energy, bio-medical, mining, telecommunications and other commercial projects. His thought leadership in EVMS has contributed to project management engagements around the world and has made him a sought after speaker on a wide variety of EVMS topics.